Delivering consistent quality while keeping processes streamlined is an age-old struggle. ISO and Lean methodologies help manufacturers tackle quality control and efficiency, respectively. But how do you decide which one your business needs right now?
Well, it’s a trick question. Because you don’t necessarily have to choose between them. Lean and ISO serve different purposes, but they complement each other. ISO is all about locking in processes, writing them down, and making sure they’re happening as written. Lean is about improving those processes for greater efficiency and less waste. Either can help maximize your profits.
However, you may still be wondering where to focus your energy and resources first? The answer will depend on your operation, your product, and your business goals.
The Difference Between Lean and ISO in Manufacturing
Choosing where to start between Lean and ISO starts with understanding how they’re different and (more importantly) how they can complement each other.
For starters, think of ISO as a fine-tuning. ISO helps you bridge the gap between how your business should be running on paper (according to procedures you’ve already set forth) and how it’s actually running right now. It’s about straightening and tightening up your whole operation so you know that the great ideas you’ve already had are getting a fair shot at success.
Lean, on the other hand, is less about darkening existing lines and more about drawing new ones. It’s about improving processes, usually through changing, deleting, or implementing new systems. If you know your business is running exactly as laid out in your company plan, to the letter, but you’re still not getting the results you want, it might be time for a Lean-style shake-up.
For a more technical look at the differences, here’s how we’d describe how each methodology works in application.
What Happens with ISO?
ISO helps businesses set standards for quality, safety, and efficiency. Manufacturing businesses use ISO by implementing those standards and frameworks, like ISO 9001. ISO involves establishing documented quality management systems, ensuring consistent product quality, and adherence to specific customer requirements.
Your company can also earn an ISO certification from a third party, further solidifying your commitment to quality for stakeholders.
What Happens with Lean?
Lean is all about becoming faster and lighter. It works by helping manufacturers maximize customer value while minimizing waste. Manufacturers can use Lean principles to improve efficiency, reduce costs, increase customer value, and foster a culture of continuous improvement.
Lean comes in particularly handy when tackling issues like excess waste, bottlenecks, stagnant processes, or a need for greater responsiveness to market demands.
ISO and Lean at a Glance
Use the table below to get a quick look at ISO and Lean and how they differ.
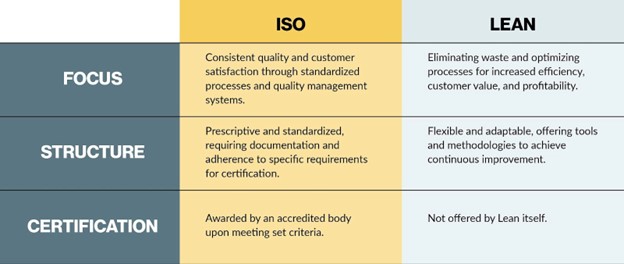
The Tell-Tale Hints in Your Operation
So now that you understand the differences between ISO and Lean, let’s talk about your business. Here are some high-level factors to consider about your operation when deciding how to phase in ISO and/or Lean optimization strategies.
- Current needs: If your primary concern is reducing waste, improving efficiency, and boosting profitability, Lean might be a better focus out of the gate.
- Customer requirements: If your customers require certified quality management systems, or you seek certification to gain a competitive edge, consider ISO 9001.
- Company culture: Lean thrives on continuous improvement and employee engagement, while ISO emphasizes standardization and documentation. Choose the one that aligns better with your existing culture.
- Resources: Implementing ISO requires dedication to documentation, record-keeping, and audits. Lean may be less resource-intensive but requires ongoing commitment to continuous improvement.
- Company size/scope of your operation: For companies with complex processes and diverse customer needs, ISO 9001’s structured approach can be a good starting point. But if you’re looking to target specific areas for improvement and cut costs, Lean’s data-driven approach can be a game-changer.
Knowing Your Product—Is Quality or Quantity More Important?
What you produce may have as much (or more) to say about whether you dive into ISO or Lean as how you produce it. Consider where your product falls on the spectrum of commodity vs. luxury. One will usually trump the other and that can give you a clue as to which development path to take. Let’s review the difference.
Commodity products (e.g., toilet paper, window panes, raw metal, and textiles) have standardized features—minimal quality variations from supplier to supplier. These items are typically marked as “essential” and consumer choices are driven by factors like affordability and accessibility. If your product is a commodity, you’ll need to prioritize efficiency in production and distribution to stay competitive.
Luxury products alternatively distinguish themselves through exclusivity, craftsmanship, and better quality. While commodity products thrive on efficiency and economies of scale, luxury products rely on meticulous attention to detail and exceptional quality to attract and retain a discerning clientele willing to invest in the elevated experience the products provide. For these companies, any compromise in quality could be disastrous. ISO can be useful here in locking down your quality assurance procedures.
Making the Right Choice for Your Operation: ISO vs. Lean
The key is to choose what works best for your company. If you already have a solid quality system, Lean might be the way to go. If you need a structured approach to quality and process control, ISO 9001 can be your foundation.
Remember, it doesn’t have to be one or the other. Lean and ISO work nicely together and you can always do both. A phased approach or combining elements from both can also be powerful. Talking to experts who understand manufacturing and quality management can also give you valuable insights and a tailored solution for your specific needs.
Takeaways
- Lean and ISO are not mutually exclusive.
- Implement Lean principles to streamline processes and reduce waste.
- ISO 9001 is a framework to ensure consistent quality and meet customer requirements.
- Many companies successfully integrate both processes to achieve operational excellence. But you don’t want to tackle too much at once.
- Start by evaluating your needs and priorities, then choose the approach that best aligns with your goals and resources. Remember, you can also consider a combination.
Next Steps
Not sure whether you need to tighten up ship or if it’s time to experiment with streamlining? iMpact Utah offers a free business assessment to get critical insights into what your business needs right now.
See how your business stacks up.